DIGITRAC.PRO
Lombarda Raccordi S.r.l.
company name
Lombarda Raccordi S.r.l.
project title
DIGITRAC.PRO
size and location
Piccola impresa, Bergamo (BG)
partner
CELS - Research Group on Industrial Systems Engineering
Logistics and Service Operations - Università degli studi di Bergamo
Exolvia S.r.l. – Spinoff dell’Università degli studi di Bergamo
UNIBG
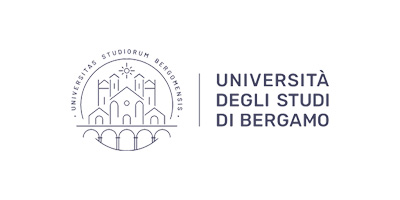
Competencies used
The problem
Lombarda Raccordi distributes copper, cast iron, brass, stainless steel, and iron fittings. One of the main challenges it has to deal with is the optimization of all production processes and to guarantee internal traceability, upstream and downstream of its activities. In fact, at the state of the art, these aspects lead to a series of inefficiencies in terms of lost time, repetitiveness, lack of information, and/or lack of traceability of the information related to the product.
To date, in fact, all phases, including purchase management, are managed manually. This approach increases processing times, with possible delivery delays, but also to a reduction in the number of batches supplied per unit of time.
This management inevitably leads to cost increase caused by ‘non-value added’ operations and to a potential quality reduction of the service offered to the market. The criticalities encountered can be summarized as follows:
loss of information and failure to create a data history;
Increase in the costs caused by “non-value added’ operations;
Increase in product returns caused by incorrect preparation in the picking phase given the lack of continuous monitoring of processes in Lombarda Raccordi.
Solution
Technologies and methods
Analysis and mapping of the current management process of the 16.000 references in the warehouse;
Formalization of the main criticalities found;
Mapping of the handling flows and determination of the average times for the realization of the output;
Re-engineering of the logistic-production processes;
Introduction of systems and technologies able to guarantee the traceability of the operations
Implementation and validation of what has been implemented in the field;
Mapping of handling flows and determination of the average times for the realization of the output to verify the benefits of what has been implemented.
The solution provides a re-engineering of the processes and tools utilized to guarantee efficiency and quality of the service provided as well as an information digitalization an integration with existing tools already in use within the company to ensure the monitoring of the production process.
Impacts
Decrease of order management times and a consequent reduction of delivery times.
Increase of the supplied quantities for unit of time with a consequent reduction of the share of fixed costs to impute on the single job order.
Reduction in the number of product returns thanks to better monitoring of the work cycle carried out.
Benefits for the company
Global costs are reduced;
Increase of the customer service quality, with the guarantee of the traceability of the entire production process;
Reduction of 25% of material movements within the production site with a significant increase in competitiveness;
Increase of the market shares thanks to a reduction in the final prices displayed to the customer and a better guarantee of the quality of the production carried out.
Rassegna stampa
Sistemi & Impresa – marzo 2022
” Digital tracking dei processi di magazzino. I passi per una trasformazione consapevole”
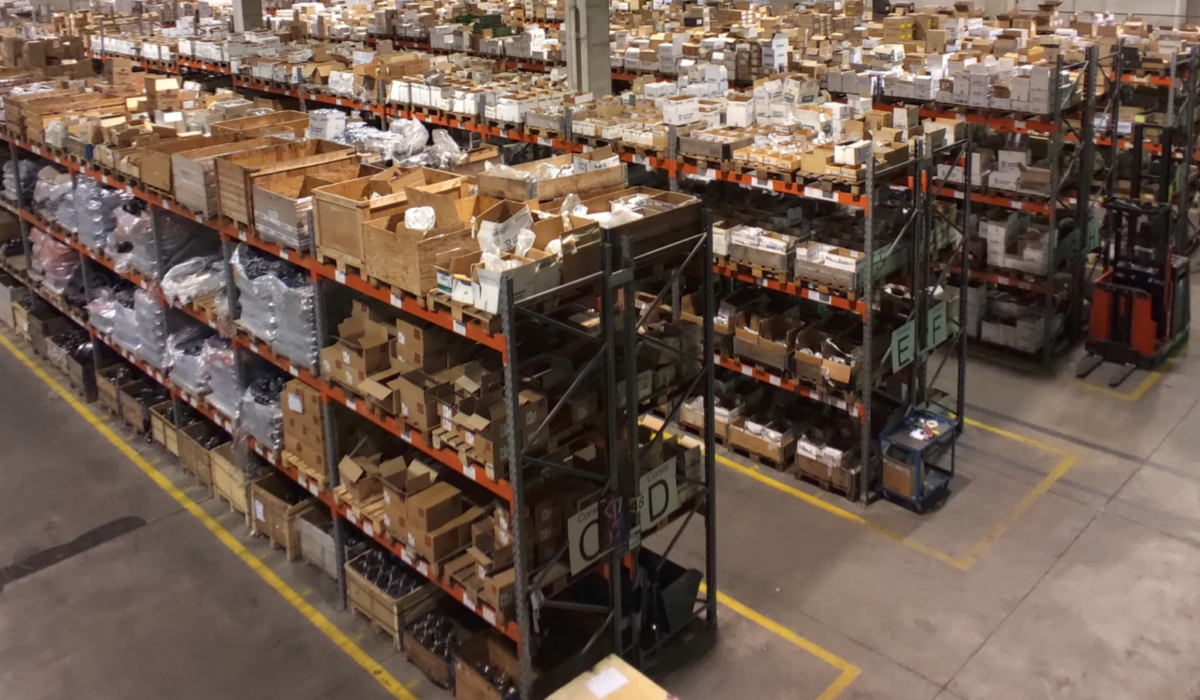
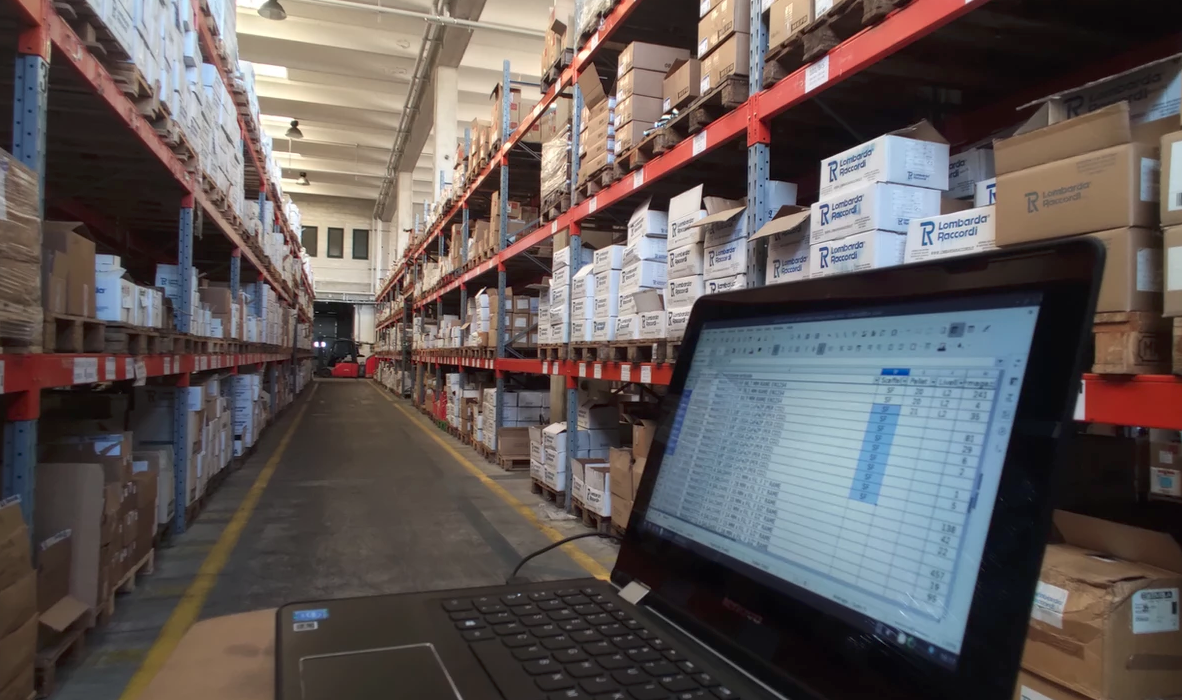
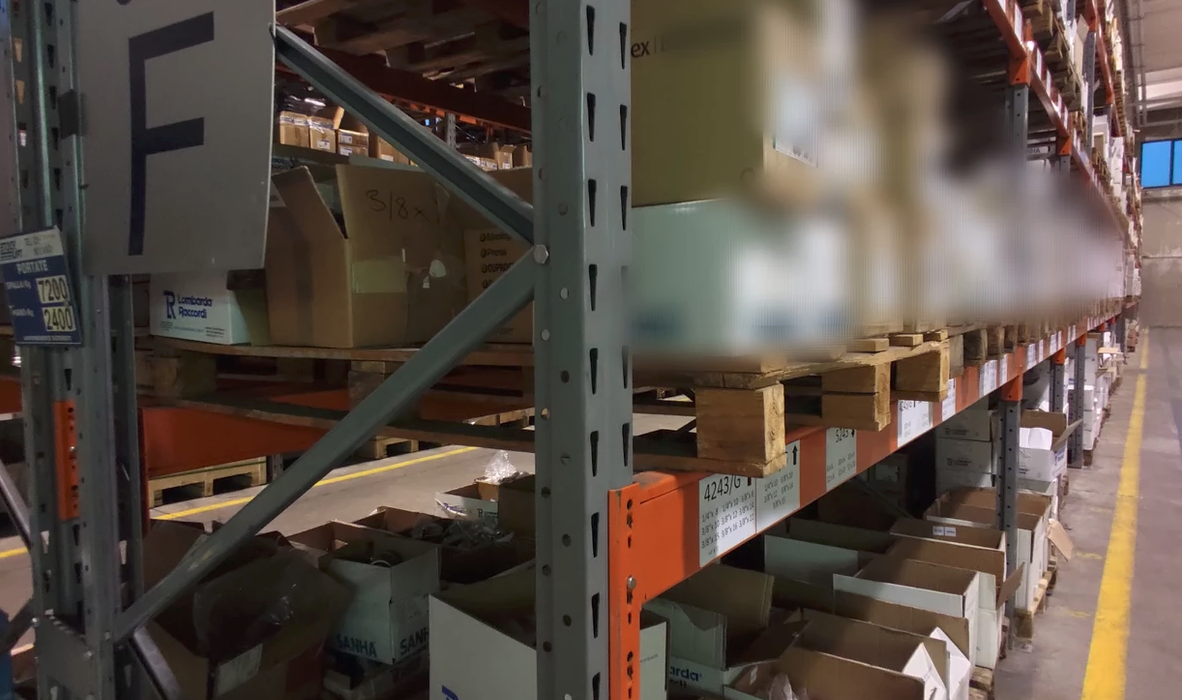