WOW
Meccanica del Sarca
company name
Meccanica del Sarca
project title
WOW
size and location
Large enterprise, Trento
partners
Comau
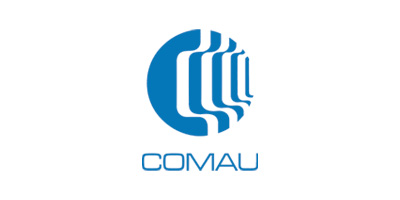
Competencies used
The problem
Meccanica del Sarca is engaged in the mechanical machining of walnut wood for the production of stocks and forends for rifles and magazines.
With the goal of expanding work space, Meccanica del Sarca planned the physical separation of two production areas: one dedicated to mechanical machining by chip removal, and the other dedicated to the painting of semi-finished wood products. This conformation, which aims to optimize production space to meet increased market demand, introduces a degree of complexity related to internal logistics: in fact, the two warehouses will rise about 100 meters apart. This entails, first, a complication in terms of handling, as an outdoor route is expected in a complex environment (slopes, mud, ice). In addition, considering the increase in production, resulting from the efficiency of the production site, and considering the need to handle the trucks manually, this choice would lead to an increase in dedicated resources with a consequent fallout in terms of unproductive costs.
Benefits for the company proposing the project
-
Efficiency of the logistics process: the implementation of intelligent AGVs with sufficient traction capacity enabling the elimination of manual activities with low added value.
-
Expansion of production capacity: the Meccanica del Sarca business plan foresees an increase in demand, which can only be met through the introduction of intelligent solutions supporting skilled operators.
-
Integration of operations processes: the AGV fleet, so designed, will imply the full integration of information systems involved in the production process such as ERP ( for order management), MES (for production progress control), production building access system and fleet control system.
Impacts
1. The identification of a mechanical solution that can provide an AGV with a traction capacity above the market standard, considering both the environmental characteristics and the condition of the route. The solution will need to be able to withstand the presence of storm water, even abundant, and cold temperatures.
2. The identification of a system equipped with sensor technology, an M2M communication protocol and artificial intelligence algorithms that ensures the possibility of automated integration of the internal logistics process with the implication of zeroing out the use of human resources for manual inbound logistics activity, thus being able to devote them to higher value-added activities.
Technologies
1. Development of prototype of an AGV (Augmented Guided Vehicle) capable of operating and reliably in both indoor and outdoor environments . The logistics modules will have to travel a distance of at least 80-90 meters in the open field in all weather conditions and about 40-50 meters inside buildings;
2. Artificial Intelligence capable of enabling the AGV to cover different routes in contiguity with people, passing vehicles, and obstacles that may be present on the route (parked vehicles, transient material depots, etc.); fleet management algorithms are expected to be used to activate alternative route strategies in order to conclude the mission in any condition;
3. IoT and Machine2Machine (M2M) solutions needed to enable the AGV steering system to be able to keep track of the route and open/close access gates to buildings in the right ways and at the right times to ensure the mission. In addition, it is planned to introduce a set of sensors that are able to detect not only the presence of obstacles, whether stationary or moving, but can also assess external weather conditions (temperature, rain, snow, ice). In this way, all the information needed to plan different mission strategies is communicated to the artificial intelligence system, with the goal of always completing the mission.
The solution, in the lean production perspective of limiting the amount of unproductive costs and non-value-added activities as much as possible, included a feasibility study for the design of a prototype AGV that is able to deliver the material exactly in the area where the operation on the production cycle is planned, to dialogue with other actors involved in the production cycle (machines, people, information systems) and to overcome physical obstacles such as, for example, non-industrial pavement or atmospheric agents typical of the alpine climate characteristic of Trentino (snow, ice, wind, etc.).
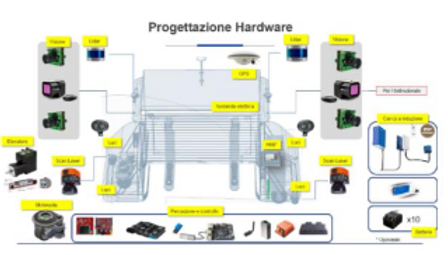
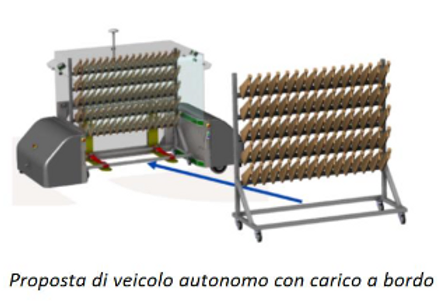