BCU (Basic Control Unit) – Carel line evolution
Implementation of a production line for the assembly of electronic products to maximize productivity.
company name
CAREL Industries S.p.A.
business size and localization
Large enterprise, Piove di Sacco (PD)
partner
Politecnico di Milano
technologies
The problem
CAREL is one of the world’s leading manufacturers of control solutions for air conditioning, refrigeration, and heating, and of systems for humidification and adiabatic cooling. The company’s historical path has, over time, included the progressive development of electronic and mechanical technologies in which a very advanced degree of development has already been achieved. Within this context, CAREL has the need to develop – with the same degree of technology/innovation – the assembly part of a new technology (THT – Through Hole Technology) and the related production process including electrical testing, assembly of plastic and elastomeric materials and visual inspection.
At present, however, the current state of the line involves labor-intensive product assembly. The project idea, therefore, aims to evaluate the introduction of automation systems in order to make the assembly process more efficient while ensuring a high level of customer service in terms of quality and waiting time.
The project aims at the theoretical and practical realization of a production line for the assembly of electronic products that, taking advantage of innovations related to the integration of different production equipment, digitization of information, and automation of functions, maximizes productivity in terms of pieces/hour and minimizes the difficulty and quantity of manual processing. Starting with the current production line prototype that is able to produce the full range of the specific product family in the “One Piece Flow” mode, the need is to maintain this important functionality offered to the market and to minimize production costs.
The solution
Technologies:
- Conceptual modeling: the line was modeled conceptually, reproducing the main production steps, material flow, semi-finished product accumulation points, rework flows, and labor behavior on the line.
- Discrete-event simulation model for conducting a comparative analysis of several alternative scenarios of the production process in terms of configuration, balancing, sizing, automation technologies, productivity, and related investment costs.
- A digital twin of the production line for the realization of a virtual scenario in which to evaluate operational parameters (productivity, execution speed, takt time, one-piece-flow, and amount of manual processing) and physical parameters of different automation solutions pertaining to the theme of Industry 4.0, such as collaborative robots and automation line solutions.
In order to reach the objective, a method was suggested that began with creating a digital tween of the production line being examined. In a second step, the project led to identifying different scenarios of interest, carrying out their simulations, identifying the most suitable line configuration, and identifying technology suppliers that could meet the requirements of the production scenario deemed most satisfactory.
Impacts
- The creation of a virtual simulation model capable of enabling the implementation of a feasibility study of an assembly production line investment. Specifically, the solution is able to identify the configuration and related investment required to achieve the desired production performance.
- The realization of a digital twin model of the entire production line, which, will also be used as a control system, providing the ability to monitor in real-time indicators with which to assess the actual degree of optimization of the assembly process.
- Definition of “what-if” scenarios: starting from the critical points detected by the current configuration of the assembly line, scenarios of interest were identified. Each scenario represents a potential change in the production line. These changes, which may relate to operator positions and tasks, automation of moving material from one station to another, automation of loading and/or unloading of a station, or automation of an entire production step, can be analyzed for potential future upgrades.
Benefits for the enterprises
- Implementation of a functional production system simulation model to support the assembly step optimization process.
- Introduction of a suitable methodology to manage the design and evaluation phase of technological investments related to automation solutions to be included in the factory.
- Increase of internal skills in terms of simulation applied to production flows.
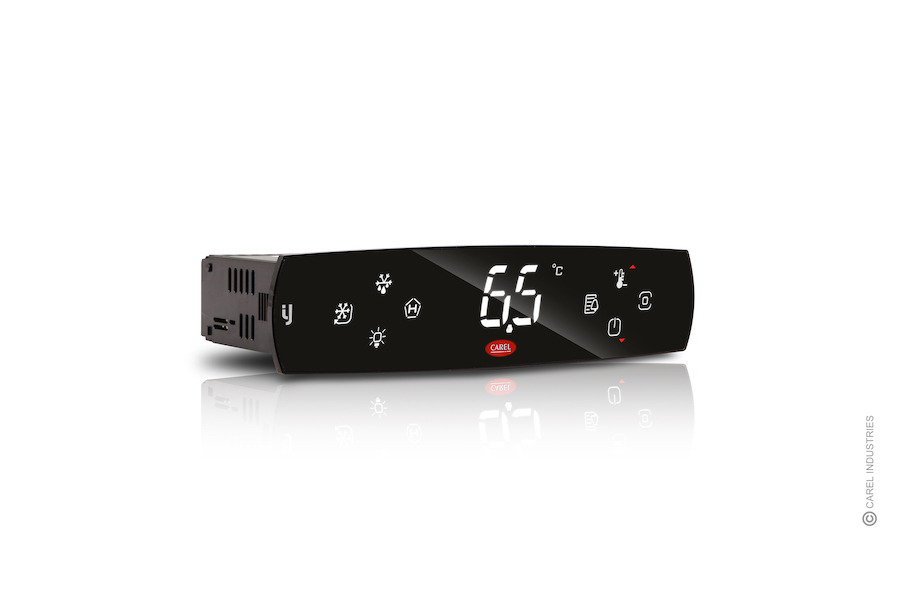