BCU (Basic Control Unit) – Evoluzione linea Carel
Realizzazione di una linea di produzione per l’assemblaggio di prodotti elettronici per massimizzare la produttività.
nome dell'impresa
CAREL Industries S.p.A.
dimensione e localizzazione
Grande impresa, Piove di Sacco (PD)
partner
Politecnico di Milano
competenze utilizzate
Il problema
CAREL è uno dei principali produttori mondiali di soluzioni di controllo per condizionamento, refrigerazione e riscaldamento e di sistemi per l’umidificazione e il raffrescamento adiabatico.Il percorso storico aziendale ha previsto nel tempo lo sviluppo progressivo di tecnologie elettroniche e meccaniche in cui è già stato raggiunto un grado di sviluppo molto avanzato. Ciò detto, CAREL ha la necessità di sviluppare, con lo stesso grado di tecnologia/innovazione, la parte di assemblaggio di una nuova tecnologia (THT – Through Hole Technology) e del relativo processo di produzione comprensivo di collaudi elettrici, assemblaggio materie plastiche ed elastomeriche e ispezione visiva.
Al momento, però, lo stato attuale della linea prevede un montaggio del prodotto con elevato contenuto di manodopera. L’idea progettuale, pertanto, ha l’obiettivo di valutare l’introduzione di sistemi di automazione al fine di efficientare il processo di assemblaggio garantendo un elevato livello di servizio al cliente in termini di qualità e tempi di attesa.
Il progetto ha come obiettivo la realizzazione teorica e pratica di una linea di produzione per l’assemblaggio di prodotti elettronici che, sfruttando le innovazioni relative all’integrazione tra le diverse attrezzature di produzione, la digitalizzazione delle informazioni e l’automazione delle funzioni, massimizzi la produttività in termini pezzi/ora e minimizzi la difficoltà e la quantità delle lavorazioni manuali. A partire dal prototipo di linea di produzione attuale che ha la possibilità di produrre la gamma completa della famiglia specifica di prodotto nella modalità “One Piece Flow”, la necessità è di mantenere questa importante funzionalità offerta al mercato e di minimizzare i costi di produzione.
La soluzione
Tecnologie:
- Modellazione concettuale: la linea è stata modellata dal punto di vista concettuale, riproducendo gli step principali di produzione, il flusso di materiale, i punti di accumulo di semilavorati, i flussi di rilavorazioni e il comportamento della manodopera sulla linea.
- Modello di simulazione ad eventi discreti per la realizzazione di un’analisi comparativa di diversi scenari alternativi del processo produttivo in termini di configurazione, bilanciamento, dimensionamento, tecnologie di automazione, produttività e relativi costi dell’investimento.
- Digital twin della linea produttiva per la realizzazione di uno scenario virtuale in cui valutare parametri operativi (produttività, velocità di esecuzione, takt time, one-piece-flow e quantità di lavorazioni manuali) e parametri fisici di diverse soluzioni di automazione afferenti al tema di industria 4.0, quali robot collaborativi e soluzioni di linee di automazione.
Per raggiungere l’obiettivo, è stato proposto un approccio che ha previsto in primo luogo la costruzione di un gemello digitale per la linea produttiva oggetto dell’analisi. In un secondo momento, il progetto ha portato a individuare diversi scenari di interesse, realizzarne le relative simulazioni, identificare la configurazione della linea più idonea e individuare i fornitori tecnologici in grado di soddisfare i requisiti dello scenario produttivo ritenuto più soddisfacente.
Impatti
- La realizzazione di un modello di simulazione virtuale in grado di abilitare la realizzazione di uno studio di fattibilità di un investimento di una linea produttiva di assemblaggio. In particolare, la soluzione è in grado di identificare la configurazione e il relativo investimento necessari per raggiungere le performance di produzione desiderate.
- La realizzazione di un modello di digital twin dell’intera linea produttiva, che, verrà utilizzata anche come un sistema di controllo, fornendo la possibilità di monitorare in real-time gli indicatori con cui valutare l’effettivo grado di ottimizzazione del processo di assemblaggio.
- Definizione di scenari “what-if”: a partire dai punti critici rilevati dalla configurazione attuale della linea di assemblaggio, sono stati individuati degli scenari di interesse. Ciascuno scenario rappresenta una potenziale modifica della linea di produzione. Tali modifiche, che possono riguardare posizioni e mansioni degli operatori, automazione dello spostamento di materiale da una stazione all’altra, automazione del carico e/o scarico di una stazione, o automazione di un intero step produttivo, potranno essere analizzate per potenziali aggiornamenti futuri.
Benefici per l'impresa
- Implementazione di un modello di simulazione del sistema produttivo funzionale a supportare il processo di ottimizzazione della fase di assemblaggio.
- Introduzione di una metodologia idonea con cui gestire la fase di design e di valutazione degli investimenti tecnologici relativi alle soluzioni di automazione da inserire in fabbrica.
- Incremento delle competenze interne in termini di simulazione applicata ai flussi produttivi.
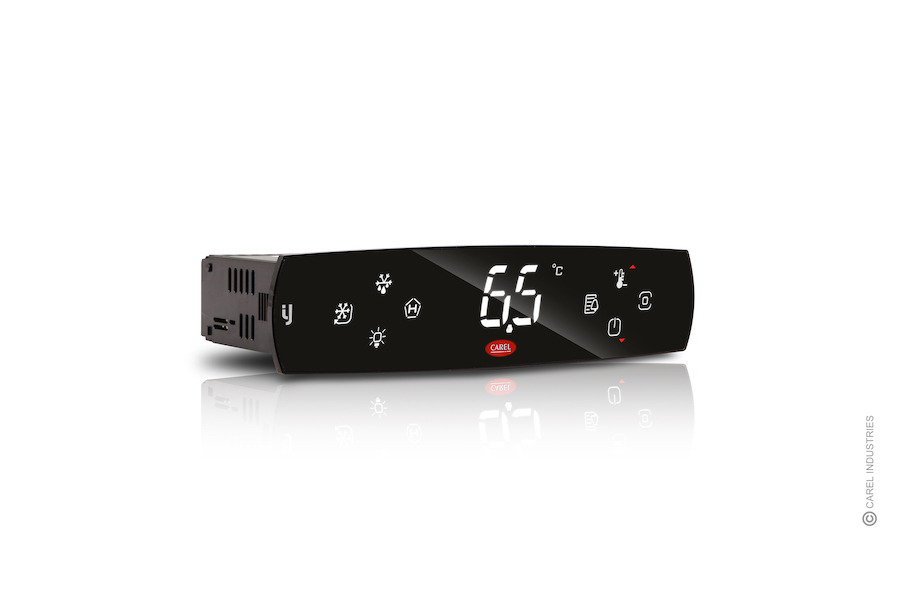