VIR-PRO-DE
Tecnoinox
(VIRtual PROduct DEvelopment) – Data virtualization and data sharing during the product development process.
company name
Tecnoinox
project title
VIR-PRO-DE
size and location
Medium enterprise, Pordenone (PN)
partnerS
Politecnico di Milano
VIR-PRO-DE
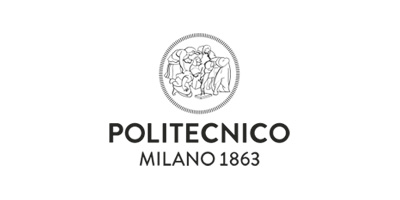
Competencies used
The problem
Benefits for the company proposing the project
Better efficiency in the management of design and new product development processes;
Less deviation between functional, technical and aesthetic requirements requested by customers with those actually developed;
Greater ergonomic impact of new designed models;
Repositioning of the company in the competitive landscape: through the enabling technologies for industry 4.0 Tecnoinox gains a competitive advantage through the opportunities enabled by digital design, PLM and Virtual Reality applied to product design and engineering.
Impacts
The implementation of PLM allows the company to manage digitally and on a single platform all the data it needs to design and govern new product requests (the new kitchens required by restaurants) and related orders.
The virtualization of the new kitchens through Virtual Reality within the CAVE (a technology that, through the projection on 4 screens of the digital twin of the product) allows an immersive visualization and a realistic experience of using the kitchen. This gives the opportunity to gather technical, functional and aesthetic feedback by interacting directly with the virtual prototype, without having to make the physical one;
The realization of the digital twin of the fryer inserted in a virtual kitchen allows the engineers in the technical department and the users (the cooks) to replicate an application scenario in a virtual environment by enabling the possibility of analyzing the ergonomic impacts of the components of the entire kitchen.
Technologies
PLM (Product Lifecycle Management) system required for integration of designs, CAD models and all information needed to manage the entire product lifecycle;
CAVE (Cave Automatic Virtual Environment) for virtualization of technical drawings;
Digital twin of individual kitchen components.
The proposed approach focused on the application of a digital twin of a fryer by identifying two development phases:
– Identification and Introduction of the enabling prerequisites for the digital twin (digitalization of technical designs, presence of an accurate 3D CAD solution, simulation of testing processes etc.)
– Virtualization of the fryer model itself in virtual reality.
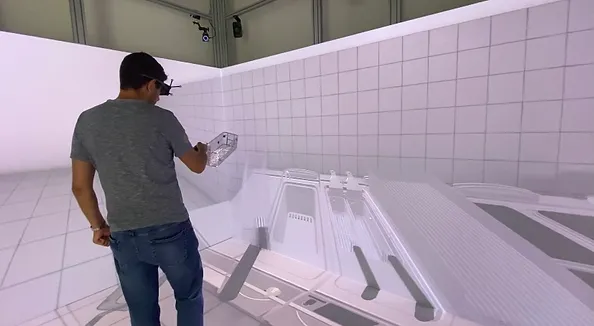
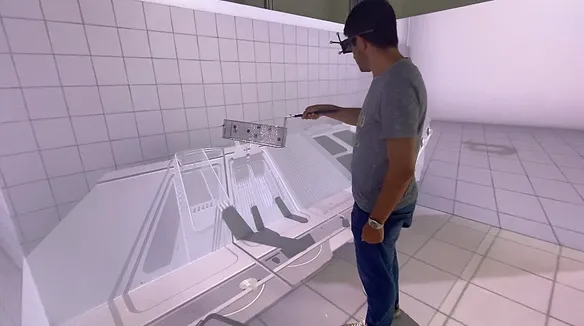