EDAP
Robby Moto Engineering S.r.l.
Il sistema proposto consiste nel supporto nella definizione e progettazione di una stazione di assemblaggio. Integrandosi con i sistemi informativi dell’azienda, è in grado di guidare il processo di assemblaggio di un prodotto.
company name
Robby Moto Engineering S.r.l.
project title
Kongchip
size and location
Media impresa, Lecco
partnerS
Politecnico di Milano
PTC
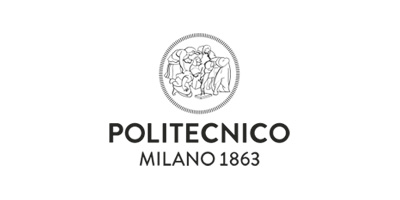
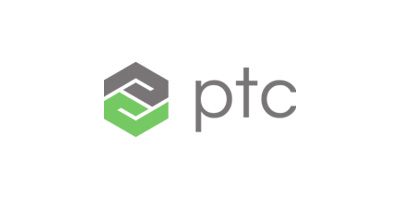
Competencies used
The problem
The project will increase user safety through accurate traceability of Personal Protective Equipment (PPE).
This allows keeping their use and life cycle under control, applying a new level of depth to the requirements of European Regulation 2016/425 and the technical rules applied. This can be done by updating products, introducing traceability systems based on cloud technologies, and consequently, adapting production processes. The changes will be considerable because the production of security devices requires attention in manufacturing. Indeed, at present, a large part of Category III PPE (that protects or reduces the risk of serious or fatal injuries) is subject to controls during the production and use stage, and its “manual” traceability generates a significant amount of time and a probability of human error that could reduce the effectiveness of the PPE itself.
Solution
Technologies
1. Cloud computing for information storage and control.
2. IoT systems for computerized device traceability (via NFC).
3. Cyber security.
The computerization of the traceability of devices through NFC technology, related to a cloud database accessible from any platform connected to the internet, will significantly decrease management errors, enabling continuous monitoring of IPR status and the correct assignment, maintenance ,and control.
Therefore, the project will provide support to several players:
the PPE user, who will be able to quickly consult the data;
those who carry out inspections
the owner organization;
the distributor;
the manufacturer.
Finally, it is possible to integrate automated functions for the calculation of deadlines, minimum requirements, orders.
Impacts
Solidifies the relationship between the main players involved in the life of the PPE, from manufacturing to use:
The manufacturer will be able to upload information and to see the status of the PPE, ensuring privacy is respected;
the distributor will be able to simply access PPE specifications and notifications of recalls or market withdrawals, even applied to the individual;
the organization owning the PPE will be able to keep under control the warehouse, the employees’ equipment, the status, the stocks, the controls carried out;
the user will be able to check the PPE status updated in real-time, without altering the data and without the need for access privileges;
the inspector carrying out the controls will use what is directly provided by the manufacturer and the user without the need for transcription. In this way:
1. it is possible to inspect the PPE without having to consult a paper file;
2. data transcription errors are almost eliminated;
3. the information is updated in real-time, allowing efficient and effective control.
Benefits for the company
Improves traceability of devices, both internal and external;
Improves the perceived value of devices and simplifies the inspectors’ work, increasing competitive advantage;
Increases information availability related to product use and life cycle.
This allows:
The ability to refine the production process according to the data collected;
Communicate directly and promptly with affected users, for example in the event of a recall;
To predict the estimated market demand depending on the state of use of the product itself.
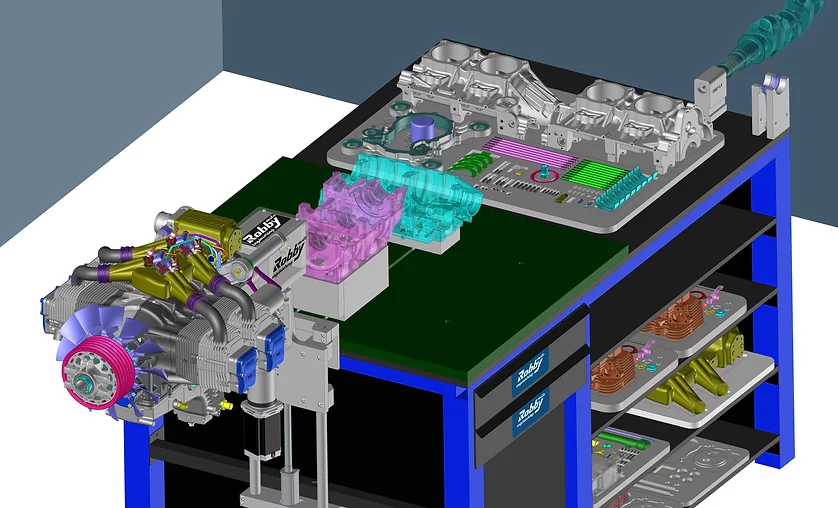
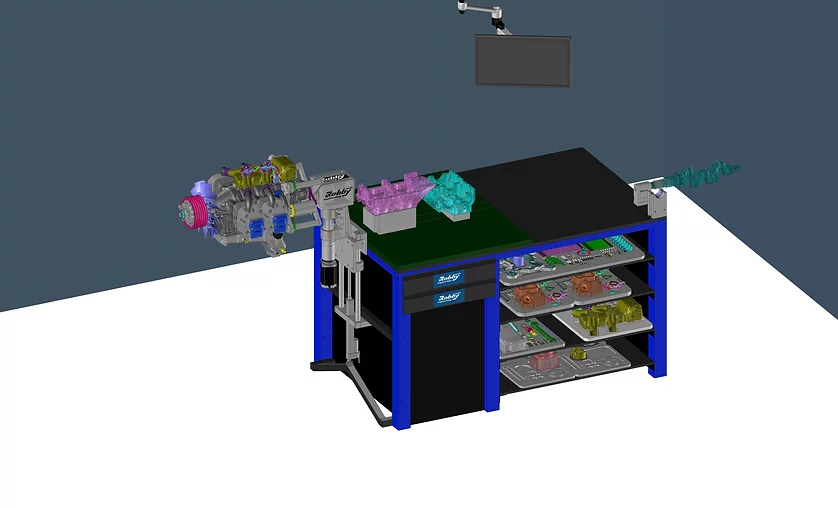
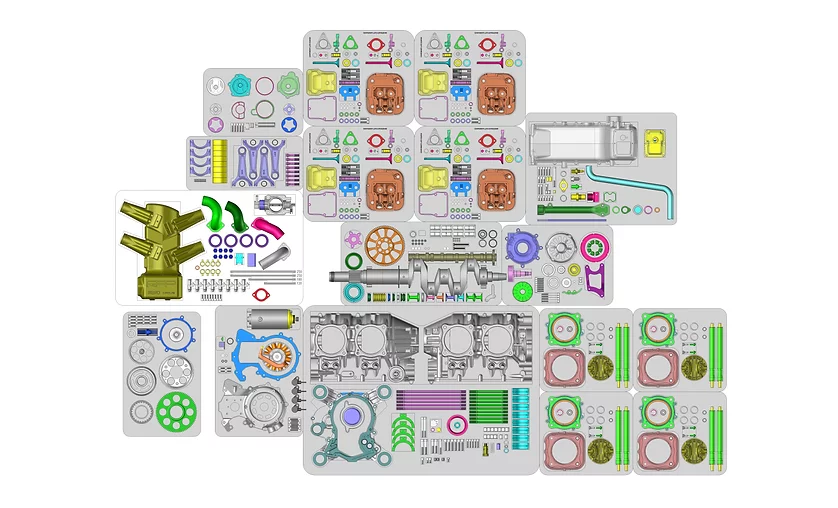
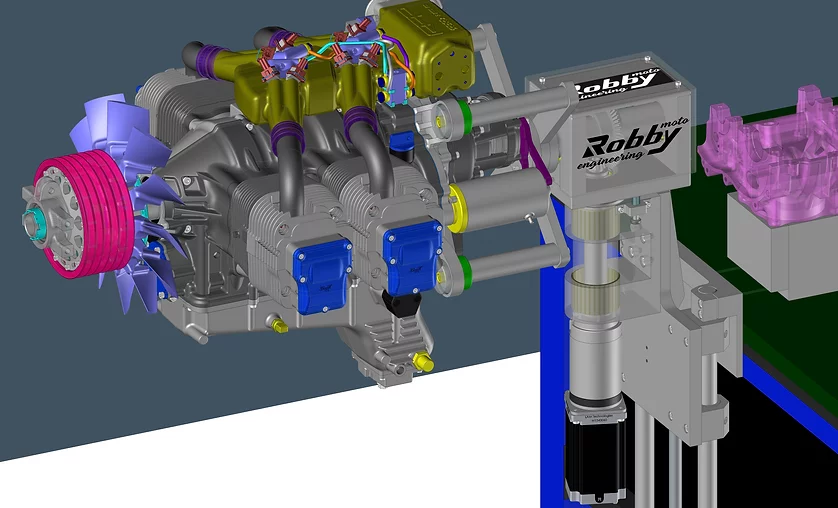